The project in this case study is the full demolition of a redundant structure, as part of the D2D – A1 DBFO Project during the Spring/Summer 2005. The structure being demolish is Holmfield Lane Accommodation bridge (Structure M62 132.00). The structure is being removed to make way for major junction improvement works – with a new structure being constructed as a replacement on the West side of the existing structure. The sub-contractor Walter Forshaw Ltd were employed by the DBFO to demolish a number of structures on the project with Holmfield being the first.
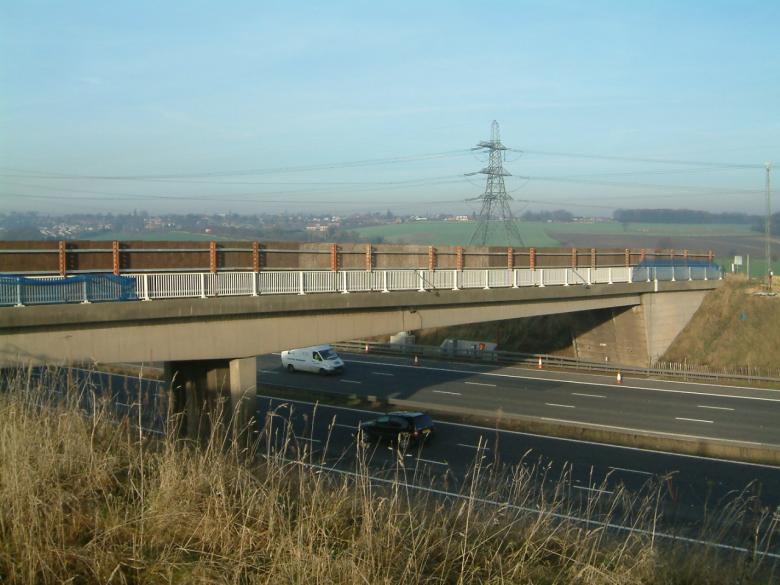
View of Holmfield Lane Bridge Dec 2004. M62 Below.
Existing Structure description.
Holmfield Lane Accommodation was constructed in 1973. The structure was closed to the general public in 2003 as part of the DBFO project and was used (after being modified with temporary hoardings) to carry site construction traffic over the busy M62 Motorway (between Jun 32 and Jun 33). The two span structure with Effective Spans 35.81m and 18.90m (with light Skew 1° 23´) had a deck width of 6.71m which was reduced to 4.5m for construction traffic with the addition of TVCB’s and timber Hoarding.
The structure takes the form of reinforced concrete cantilever and side span T-Beams with insitu in-fills. The end supports were reinforced concrete cantilever abutment on spread footing (North end) and reinforced concrete abutment on spread footing (South end). Intermediate Supports Square Reinforced Concrete Columns on Spread Footing Foundation.
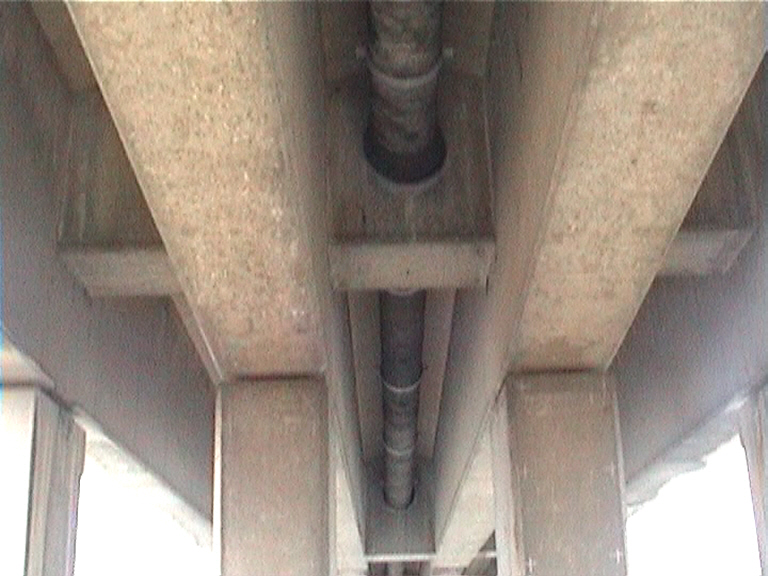
View of the bridge beams, column connection + diverted watermain.
During the course of the construction works the project carried out extensive diversion works to enable a 400mm Water Main Suspended from Deck betweens. Internal Beams and the 100mm Cable Ducts to Both Footpaths.
The bridge surfacing was made up of Dense Bitumen Macadam with Asphaltic plug joints. The deck waterproofing was identified as Baytec spray applied Membrane. The parapets were formed from non-standard - Steel P2 Parapet with Vertical Infill Bars. Paintwork to on the parapets was tested with no lead paint recorded.
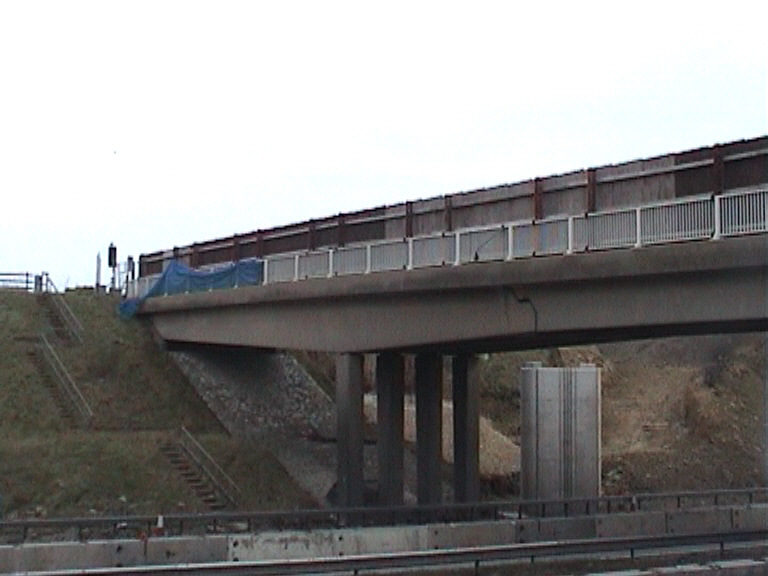
TVCB's in place down ready to be replaced with cones, New bridge column being build to the side of the existing bridge columns.
On the 7th March 2005 – Balmer Lindley removed the central reserve crash barrier – post and barrier 100m either side of Holmfield Lane Bridge. With the barriers removed, RMG Traffic Management carried out the removal of the TVCB concrete units running under the bridge and replace them with cones and rope forming a minimum 10m wide safety zone between the East & West bound traffic. This work was carried out on the 14th & 15th March 2005 night-time working.
Holmfield Lane bridge was closed to construction traffic on the 11th March 2005 this allowed access to remove the TVCB concrete units along the length of the bridge during normal working hours. The traffic lights on the bridge were also removed at the same time.
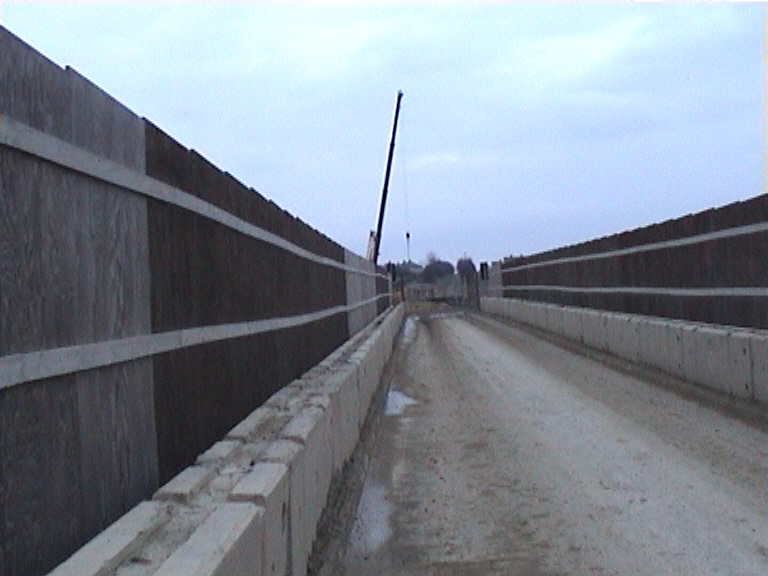
The bridge deck fitted out for site traffic - TVCB's, Hoardings and Traffic lights to keep traffic single file.
Following removal of the TVCB units the bridge was handed over to Walter Forshaw Ltd to remove the deck surfacing and removal all material from the bridge deck. A mini excavator fitted with a breaker was used on the bridge deck to break up the black top surfacing to reveal the concrete (the excavator did not peck directly above the carriageway). Once the surfacing is broken up the excavator fitted with a bucket will peel back the tarmac surfacing working its way across the bridge clearing the material into a stockpile of the end of the bridge. Where required the footpaths were broken out to gain access for drilling.
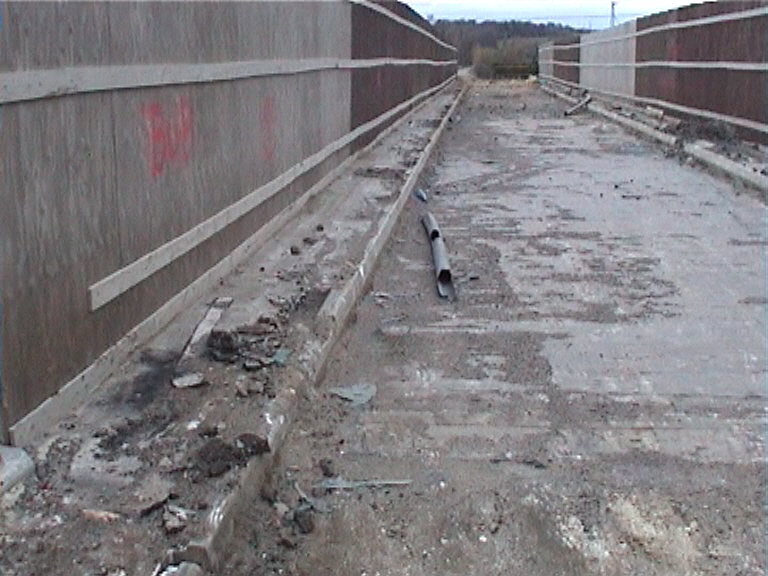
Bridge deck with TVCB's removed ready for black top removal.
With the deck surfacing removed WFL carried out pre-drilling of the deck.
WFL using rock drills carried out drilling operations -
Deck suspended section 22 nr vertical holes 1.5m deep, Deck cantilever 22 nr vertical holes 1.5m deep and 12nr vertical holes at 1.8m deep. All the drilling work was carried out from deck level during normal working hours. This work was completed by 18th March 2005 ready for charges being set on the 19th March 2005.
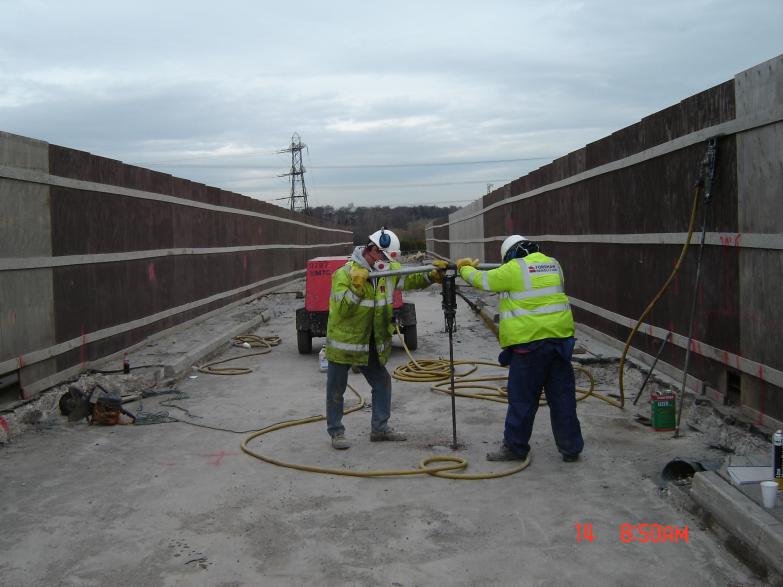
WFL drilling holes in the deck ready for Charges.
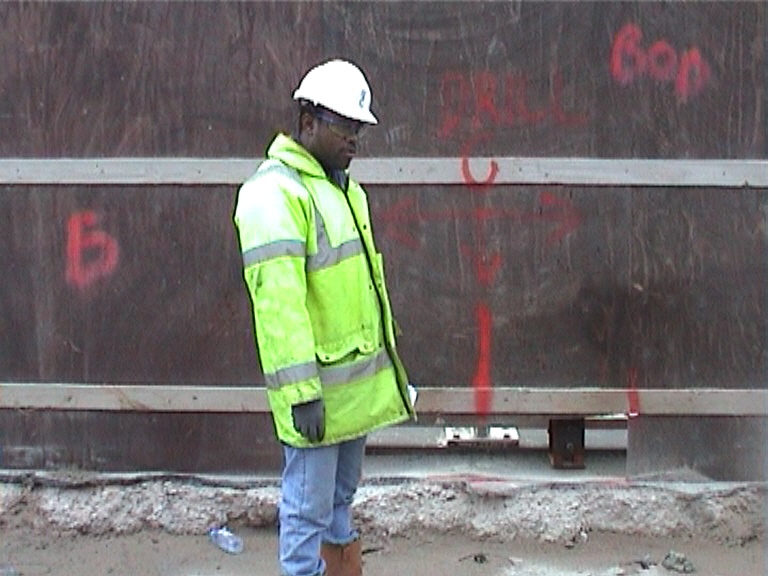
Everton McDonald - "the rasta man" - assistant engineer working for David Millar.
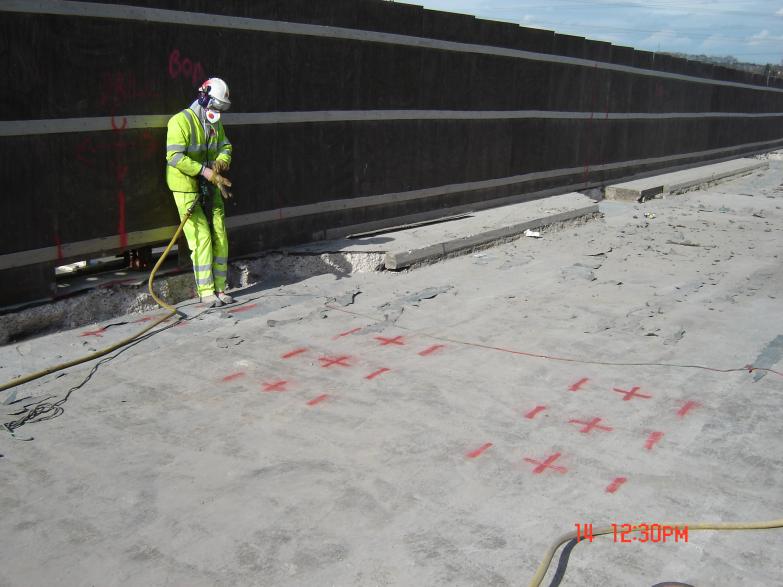
WFL operative getting ready to drill holes in the deck with heavy duty rock drill.
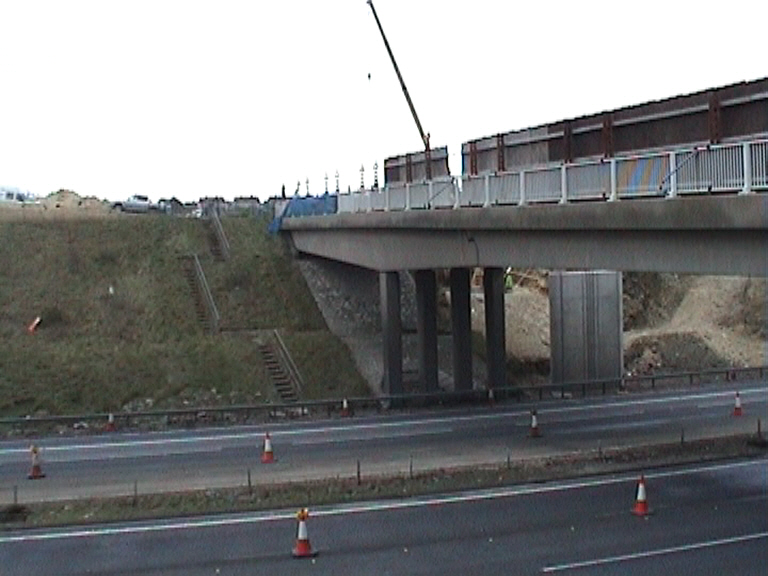
Hoardings being removed at high level - TVCB's removed
Walter Forshaw Ltd also carried out drilling to the four support columns in the West Bound verge and at locations where drilling may cause the concrete to spall. Utilising traffic management to provide a safety zone lane one and the hard shoulder over a period of three nights-shifts from 16th, 17th & 18th March 2005. WFL used scaffolding to access and carry out preparation drilling to the columns, they are also installed as much (debris containment) geotextile (monoflex) and chainlink membrane as possible with the final section over the predrilled holes not covered until after demolition charges are set during the main possession.
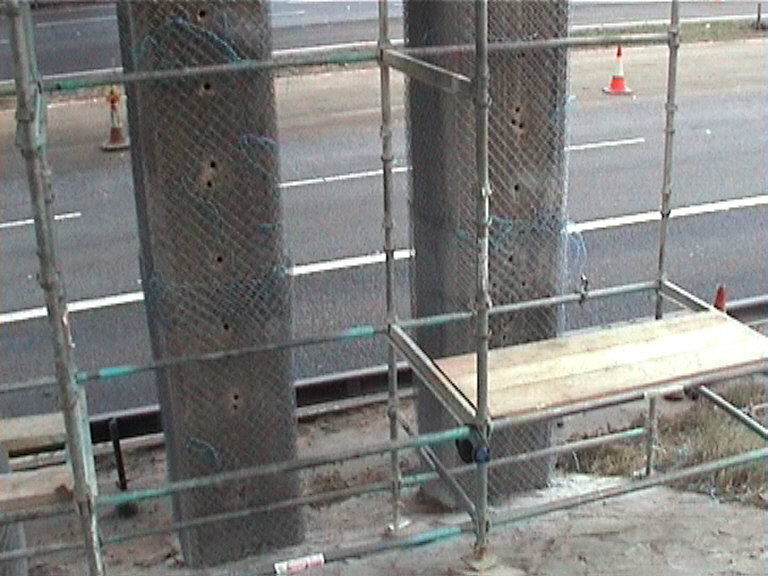
WFL drilling and wrapping the columns.
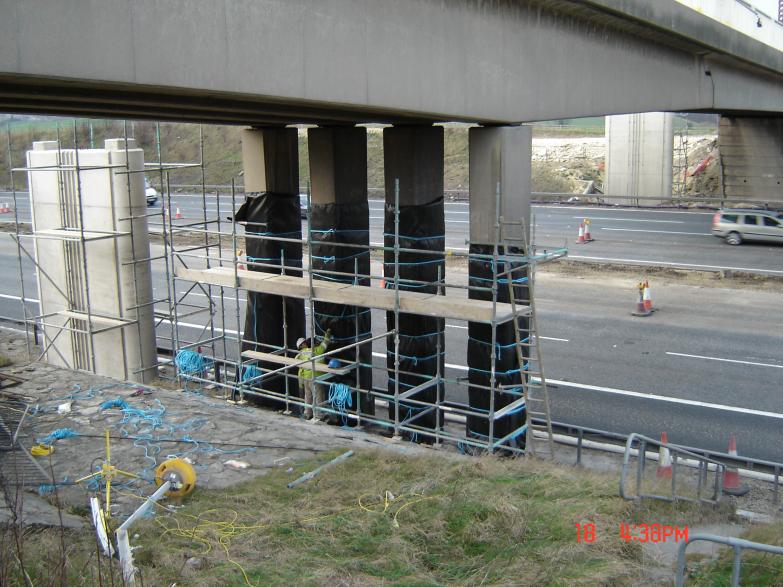
WFL operatives wrapping the columns with charges set in place.
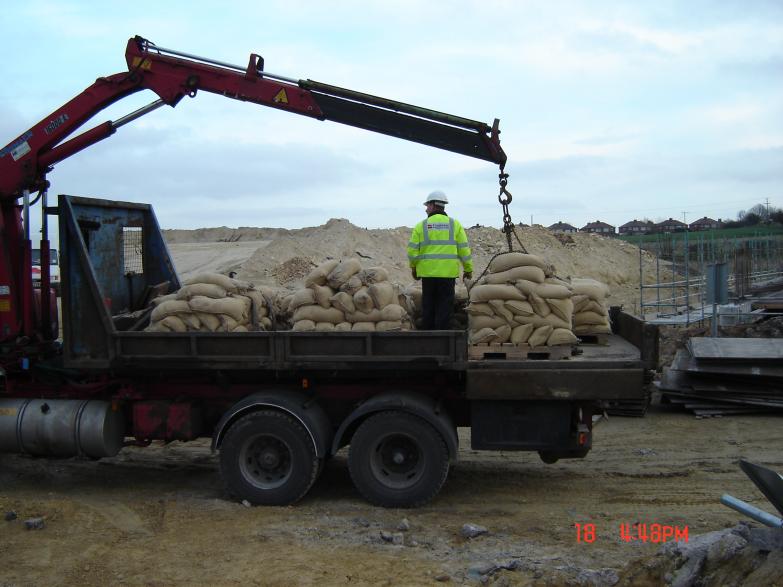
WFL operative offloading sand bags ready for protecting the charges on the deck.
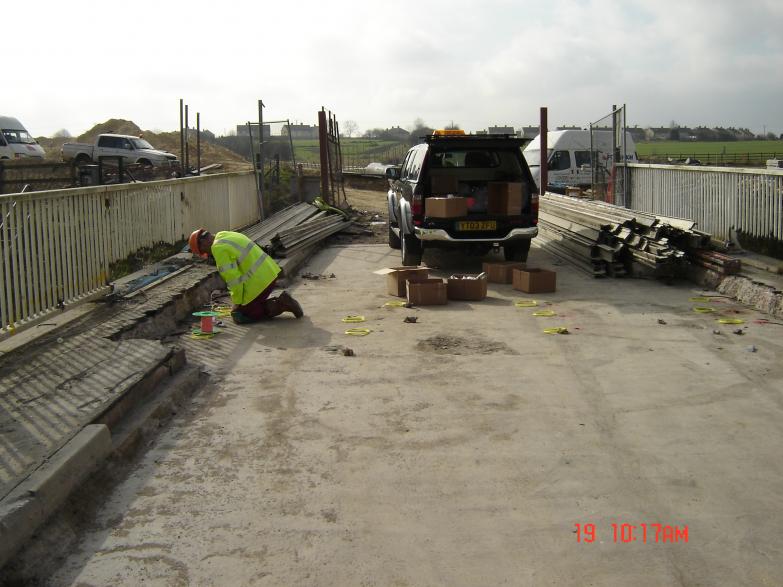
Charges being set including detonators and securely stem vertical holes with hardstop and horizontal holes with plystem.
Explosive Charge Placement: - Arrangements were made for the delivery of the required explosives in the morning before the road closure.
With the security exclusion zone in place Walter Forshaw Ltd are to start the installation of the demolition charges.
Place the explosive charges including detonators and securely stem vertical holes with hardstop and horizontal holes with plystem. Connect and link together the initiation system and lay / secure the final blast wrap materials etc.
Lay out the starter line to the control / firing position.
Follow the standard countdown procedure leading to the blowdown.
The detonation to take place subject to confirmation that the exclusion zone is maintained clear of all personnel by Walter Forshaw Ltd. appointed manager who shall liaise with RMG and others that may be affected by the detonation.
The explosives to be used will be 120g cartridges of Infernit, a NG based explosive loaded into the shot holes in quantities appropriate to displace the volume of concrete within the drilling patterns.
Non-electric detonators of the specific delays appropriate for each part of the structure would be distributed adopting a colour coding to assist in ensuring their correct locations. Initially the detonators would be placed adjacent to the holes in which they are to be loaded.
The detonators would be introduced into a central cartridge within each shot hole. Only personnel familiar with safe practices associated with this work would handle explosive charges.
Stemming will take place as a follow up operation by personnel with previous experience and training in this work. Plystem would be used for stemming horizontal holes, plugs of clay carefully and securely pushed into the ends of the explosively charges holes. Hardstop grout poured into vertical holes.
Following charge placement, all the ‘in hole’ detonator leads would be connected together using ‘e’ cord and Nonel ‘e’ clip connectors laid on the deck and covered with sandbags.
The entire non-electric detonator system would be checked to ensure continuity of primary circuit, delayed back up circuit for correct alignment and separation of detonator fuse heads to avoid any risk of shrapnel cut offs. During the explosive charge placement period access onto the structure is to be restricted to essential personnel only. During the connection of leads period, access onto the structure is to be by explosives engineers escort only.
With the security exclusion zone in place Walter Forshaw Ltd are to start the installation of the demolition charges.
Place the explosive charges including detonators and securely stem vertical holes with hardstop and horizontal holes with plystem. Connect and link together the initiation system and lay / secure the final blast wrap materials etc.
Lay out the starter line to the control / firing position.
Follow the standard countdown procedure leading to the blowdown.
The detonation to take place subject to confirmation that the exclusion zone is maintained clear of all personnel by Walter Forshaw Ltd. appointed manager who shall liaise with RMG and others that may be affected by the detonation.
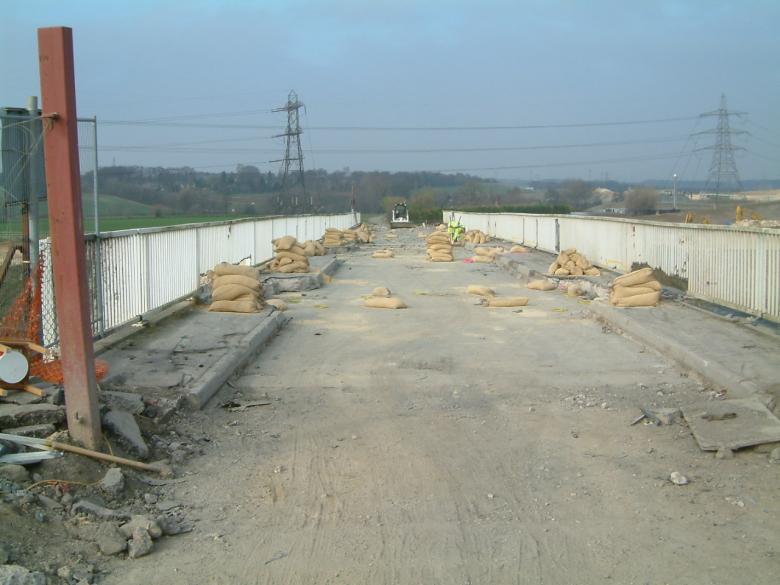
Charges being covered with sandbags on the deck.
Possession 1 - Main demolition and clear up.
The road closure of the M62 took place between -
Saturday 19th March 2005 @ 19:00 to Sunday 20th March 2005 @ 11:00 - The closure lasting 16hrs in total.
At the start of the M62 closure - RMG Traffic Management checked to ensure that a route is available from both Jun 32 & Jun 33 for emergency vehicles during the course of the M62 closure.
At 19:00 RMG traffic management closed off the M62 at Ferrybridge Jun 32 and at Glass Houghton Jun 33 – routing traffic via the agreed diversion route shutting down both the East and West bound M62 between the junctions.
Setting up the Traffic management took about 15 -20 mins. Once in place the RMG Traffic officer putting the diversion route place contacted the RMG site manager (David Millar) and give authorisation to start the possession. Traffic Police (Supplied by West Yorkshire Police) were located at the junctions on to the M62 (No 32 & No 33) to ensure that the traffic followed the diversion fully.
Three mobile lighting towers were positioned approximately 35m either side of the bridge (six in total). In addition to the six lighting towers provided for the illumination of the bridge four further lighting towers were utilised to light the exclusion zone. An agreed lighting plan was developed and agreed with RMG prior to the possession to ensure the work site was fully illuminated.
RMG carried out a letter dropped all local properties to ensure that residents are aware of the demolition work being undertaken. The main work site some distance from the nearest local residents however a farm house on the North side of the bridge is approx 200m away.
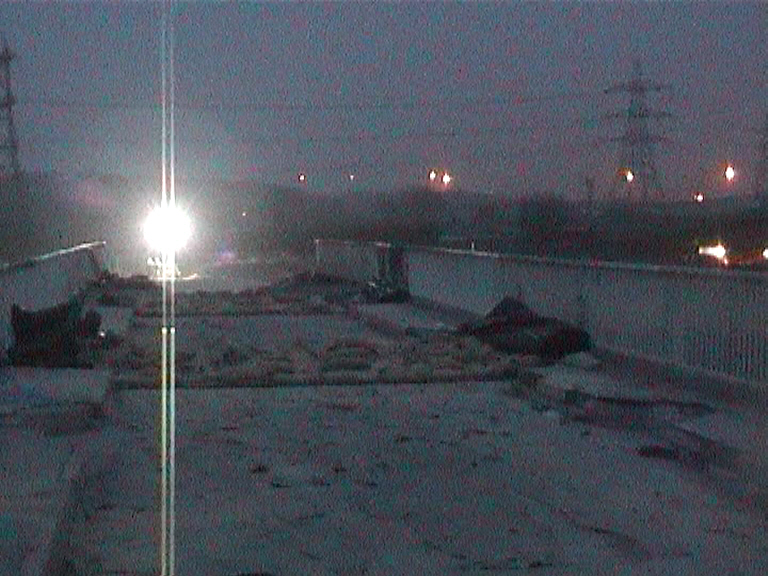
Lights set highlighting the bridge deck - Charges on the deck set ready.
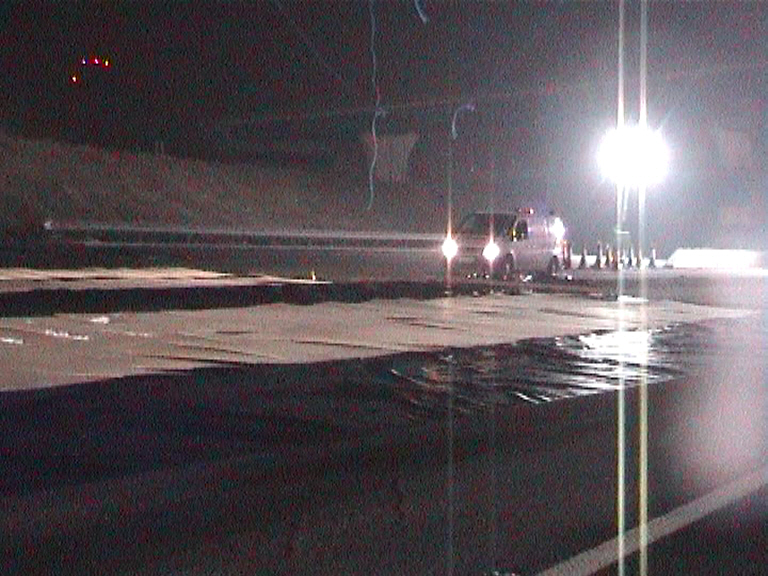
At the start of the road closure geotextile and plywood sheets were placed on the carriageway to protect the road surface.
Locally under the structure, steel plates were installed to protect the central reserve and the highways drainage to protect it from plant running down and crossing over the central reserve
The Geotextile was man-handled by operatives with the roll placed approximately 25m to one side of the bridge and rolled out under the bridge approximately 25m to the other side of the bridge. This method was used to cover the whole carriageway.
¾’’ Plywood Sheets were placed on top of the geotextile. A JCB was used to pick a pallet of plywood sheets up on its forks and slowly drive on top of the geotextile. Operatives lifted and laid sheets and place them directly on top of the geotextile.
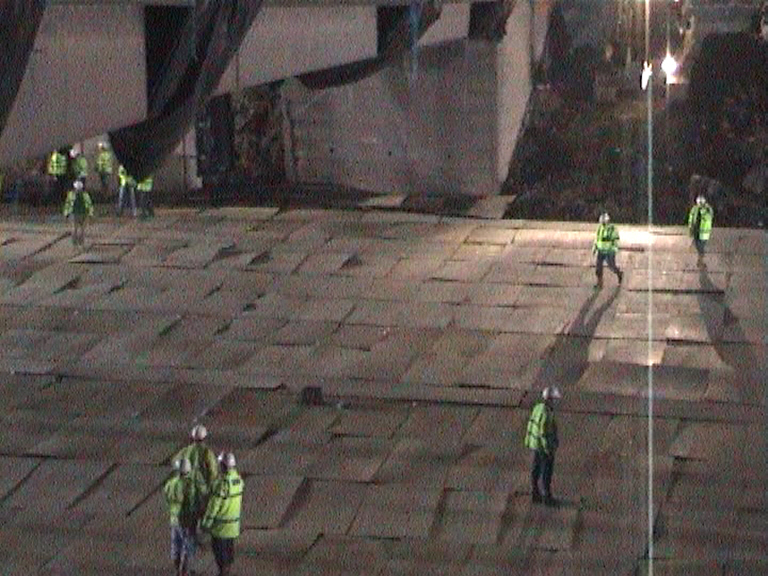
Carriageway covered with plywood sheets over the goetextile sheets.
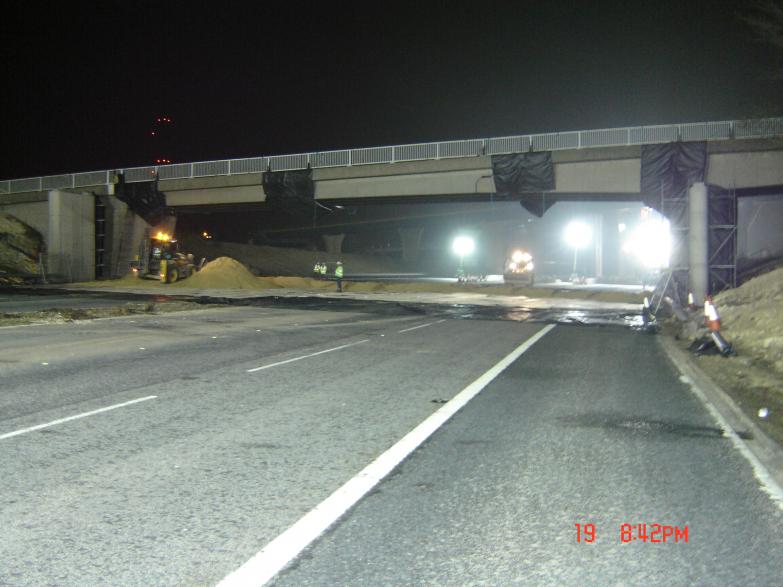
Sand being placed on top of the plywood sheet, mounds placed at each of the main blast positions.
Once the road has been protected the articulated dump trucks were reversed into position with the aid of banks-man under the bridge. Once in place they tipped the load of crushed material using the tip and run method. The crushed material was supplied from the on site process plant stockpile (located 30m north of the North Abutment). Water Forshaw Ltd loaded the Volvo dump trucks at the crushing plant. Access for the ADT’s was via the M62 at the authorised access point and run up the East bound carriage way to the bridge demolition site.
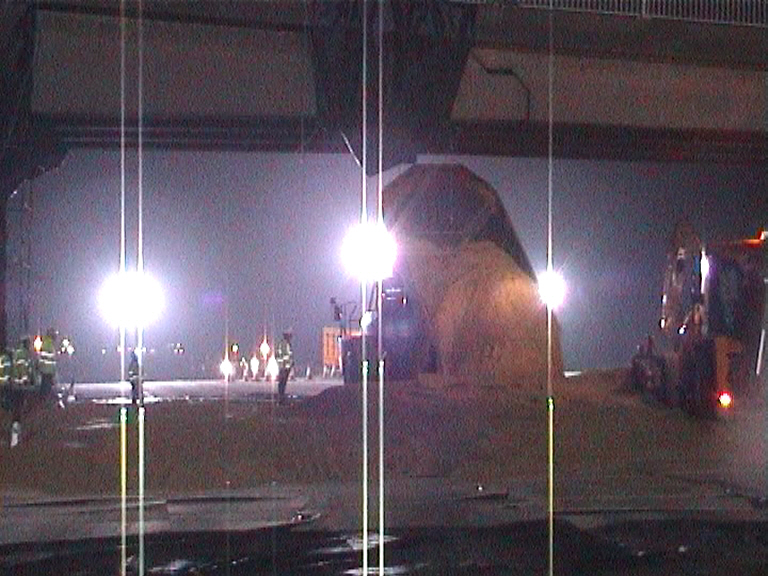
Articulated Dump truck placing sand (6f5) material - JCB shifting and creating sand mounds under the deck blast points.
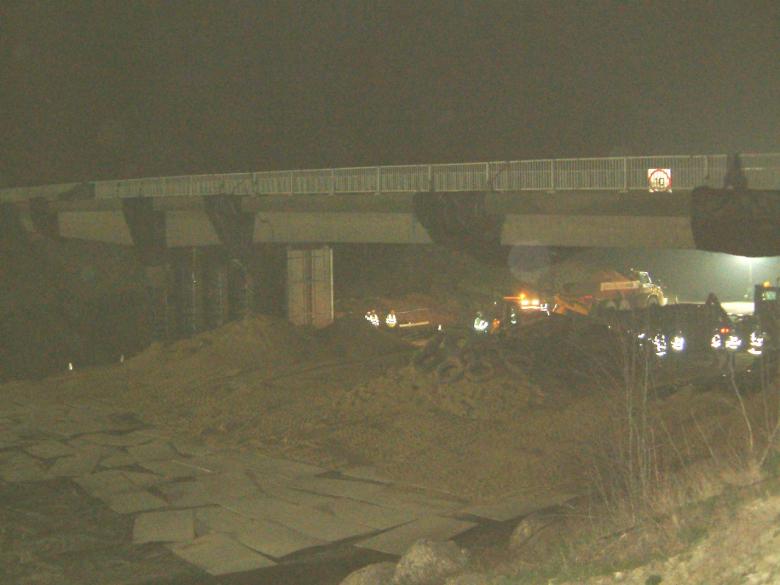
Tyres placed on top of the sand mounds to break the fall of the deck as it breaks up.
Tyres were placed on top of the crushed materials directly under the bridge. Tyres will be stored in a bin wagon and will be rolled along the ground towards the crushed material and placed on top of the crushed material directly under the bridge. The tyres were lifted into position and placed using the excavator.
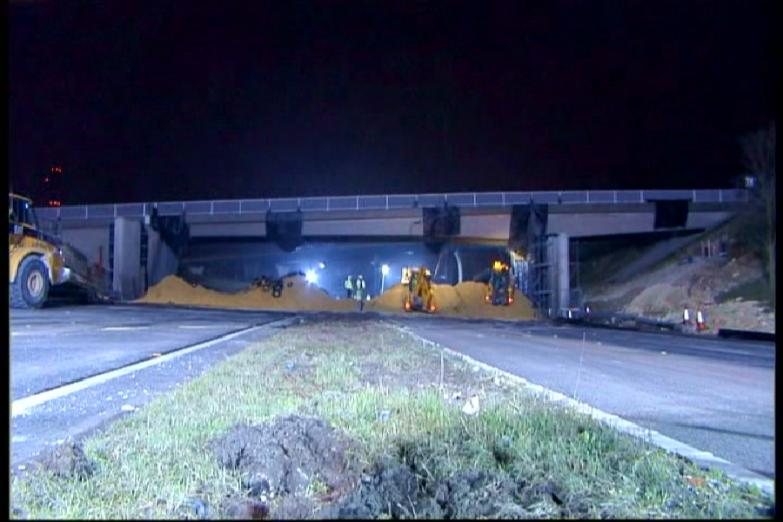
Sand being placed and formed under the deck with tyres built up on the mounds.
WFL were responsible for the implementation, management and maintenance of a security exclusion zone around the blasting area. The exclusion zone was manned by a series of operative sentries fully briefed and located around the perimeter of the exclusion zone to acquaint them with the responsibilities in readiness for the blow-down.
Extract from the Instruction to Sentries:
a) Ensure you know how to operate your radio and that it operates correctly by making regular contact with the control.
b) Take up position as instructed by the explosives engineer and marked on the exclusion zone plan.
c) Generally maintain observation of the area inside the exclusion zone and keep people outside the line of sight of the sentry either side of your position. Do not leave your position. If you see anyone encroaching into the guarded area, advise the control point by radio immediately.
d) At 5 min. prior to the felling time, upon hearing the 5 min. warning siren, the detonation is to take place unless a breach of the exclusion zone occurs. Be particularly observant and advise control if you for any reason think there is a breach of the security cordon. Be ready to respond to confirm your designated area is clear of personnel.
e) Providing all sentries confirm the exclusion zone clear, just before detonation a 10-second air horn is sounded followed by the detonation approximately 10 seconds later.
f) Maintain the exclusion zone clear until you hear the single 'all-clear' siren, which will be sounded 2 to 5 min. after the felling. Then proceed to your reduced exclusion zone position and advise people not to approach any closer.
Main Demolition phase (setting the charges)
On completion of the carriageway protection works the work area under the bridge was evacuated to enable the demolition charges to be linked and set for detonation.
Main Demolition Phase (Standard Count down procedure and detonation)
From 1 hour before the scheduled felling time. Security checks were carried out to ensure the exclusion zone is clear of all personnel.
30 mins before the scheduled felling time, sentries were sent out their positions beyond the perimeter of the exclusion zone.
5 mins before the scheduled felling time, a single 10 second air horn was sounded to alert the sentries to raise their flags or respond by radio in turn providing the exclusion zone is clear of personnel. One flag dropped signifies all flags down.
20 seconds before the scheduled felling time, with all flags are held raised, a 10 second air horn was sounded. The detonation took place approximately 10 seconds after the sound of the air horn.
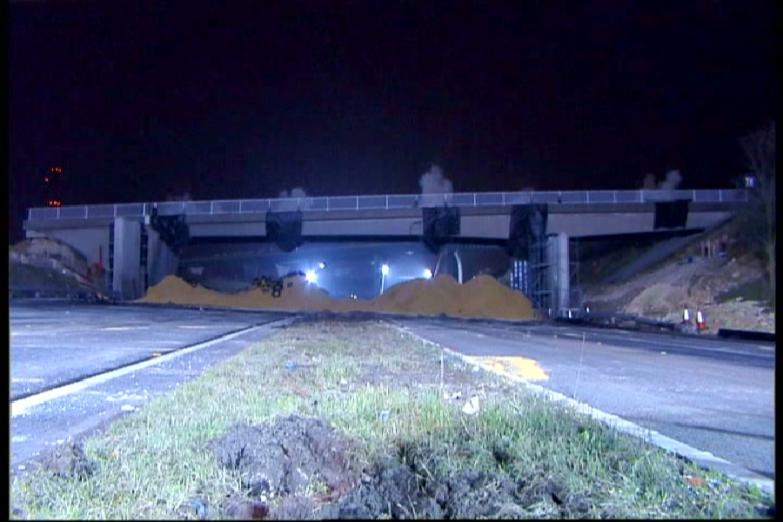
Milli-seconds after detonation. (a few minutes before midnight 19th March 2005)
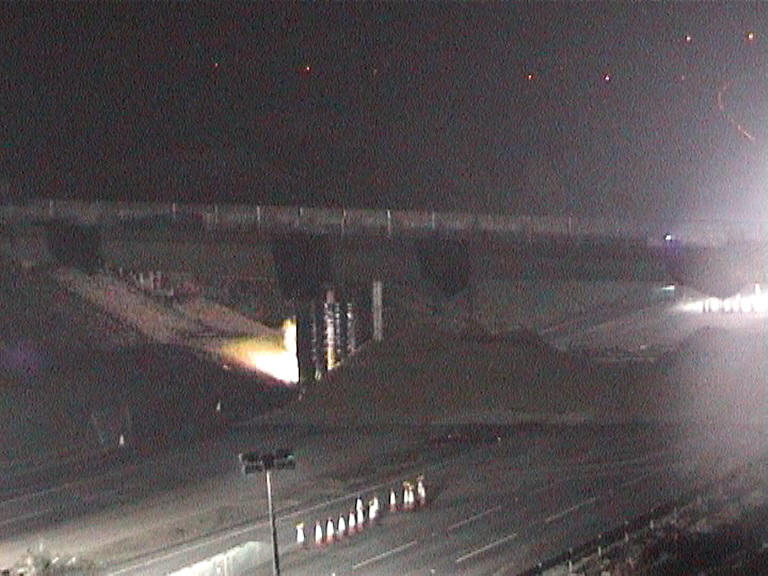
Charges in the columns are detonated to fell the columns.
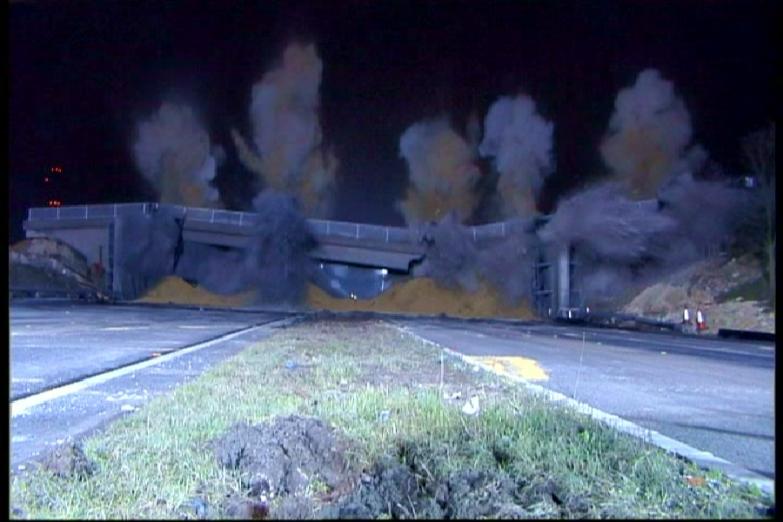
The bridge deck charges explode breaking it's back landing the bridge onto the sand mounds.
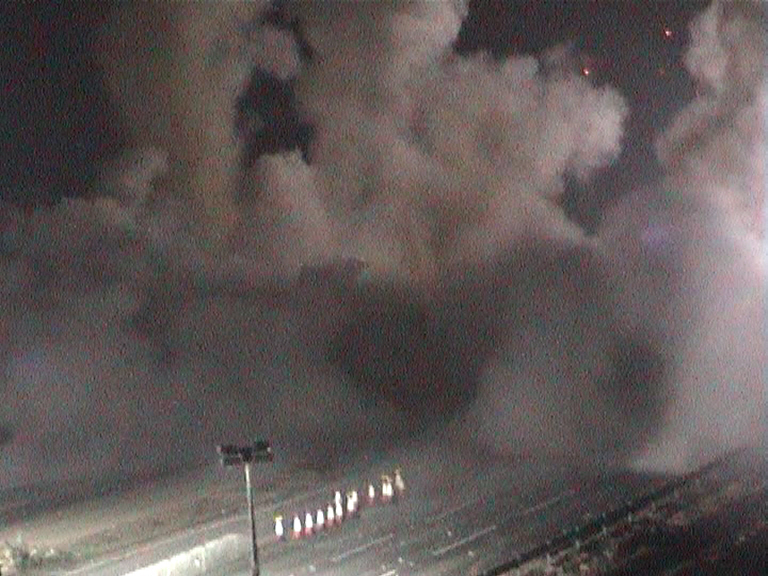
Bridge fully enveloped in Dust from the blast.
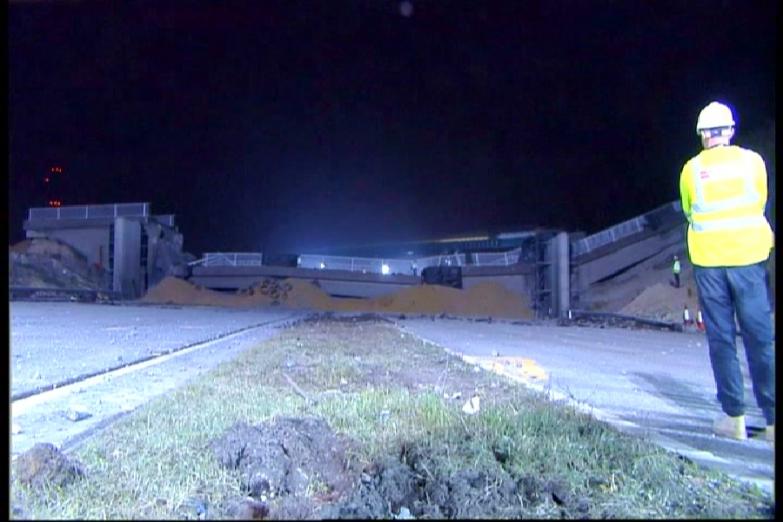
Once the dust clears - the explosives Engineer carrying out an inspection of the bridge.
2 to 5 mins after the detonation, a long air horn blast was sounded as an 'all-clear'. All persons were to maintain their positions until the Explosives Engineers have confirmed that all explosive charges have detonated and this 'all-clear' is sounded.Note: Repeat from item d) above should a breach of security occur, following the removal of intruder/intruders from the exclusion zone
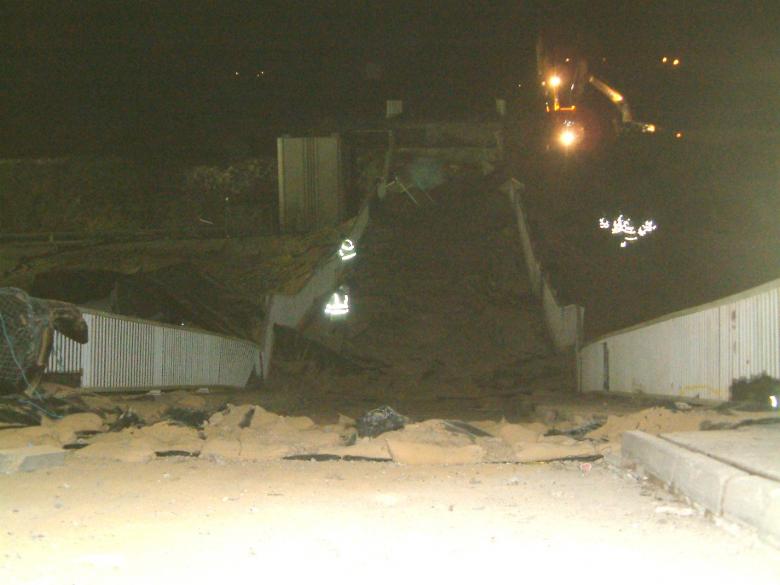
Once the deck has been cleared and checked by the Explosive Engineer access can be granted for machines to move into position.
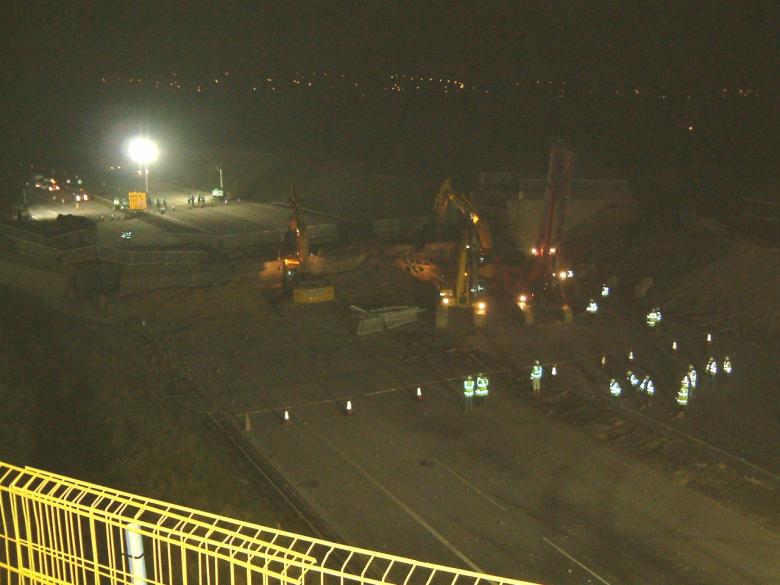
WFL exclusion zone in place - with the machines starting to rip the bridge apart.
Walter Forshaw Ltd installed a physical barrier (pedestrian fence / cones and rope) exclusion zone 30m away from the bridge on both sides.
During the machine demolition phase – WFL utilised a number of specially adapted excavators tracked onto the plywood sheets and sand covering the M62 carriage way surface. The majority of the excavators were fitted with concrete pulverisors to break up and process the concrete into manageable weights and sizes.
A long reach type excavator was also located at the bridge site to grab the bigger sizes of concrete and place them directly on the embankment storage area for processing post possession. All material placed on this side of the embankment were later crushed and either reused or removed to a licensed transfer station. The smaller materials will be placed directly into ADT’s tipper trucks and taken to a pre-determined area for processing.
Where mechanical plant is unable to process through steel reinforcement and cable strands– flame cutting with compressed gas Oxy-propane cutting equipment to burn through reinforcement steel and tendon strands.
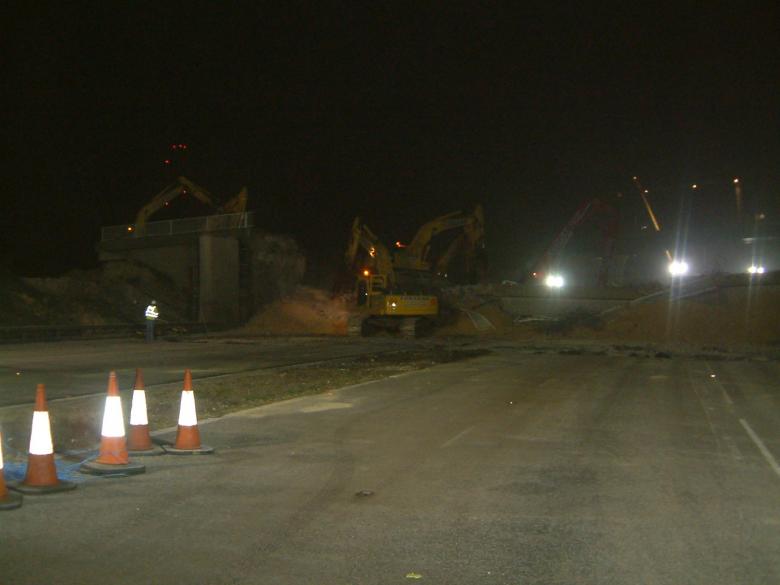
Excavators ripping into the bridge deck breaking up the concrete and loading into ADT's.
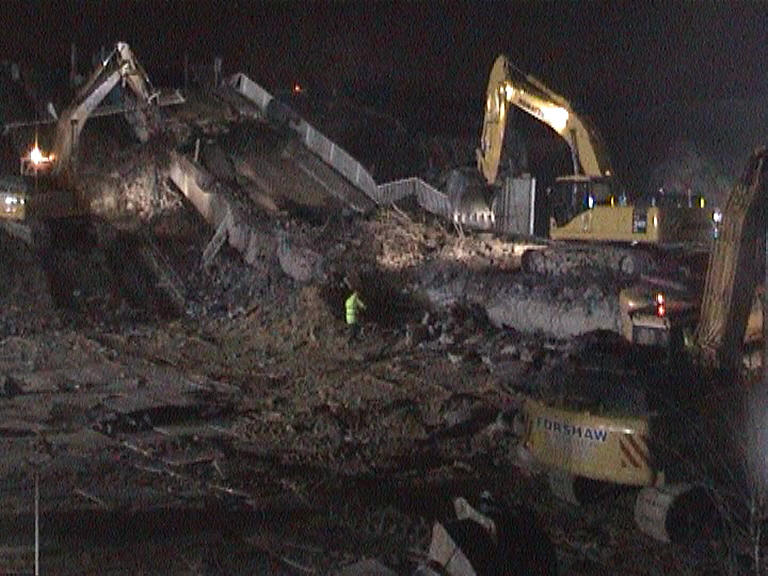
02.00 Excavators ripping into the bridge works concentrated on the section blocking the M62.
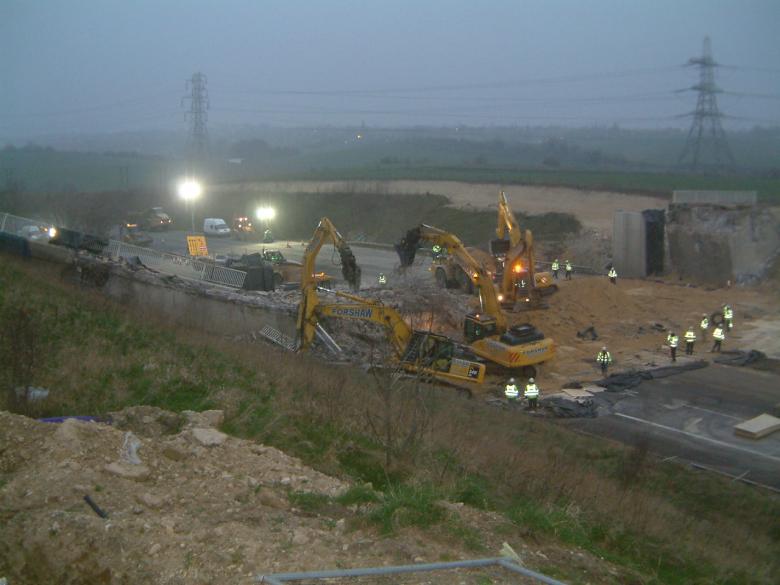
07.00 majority of the bridge deck on the road has been cleared.
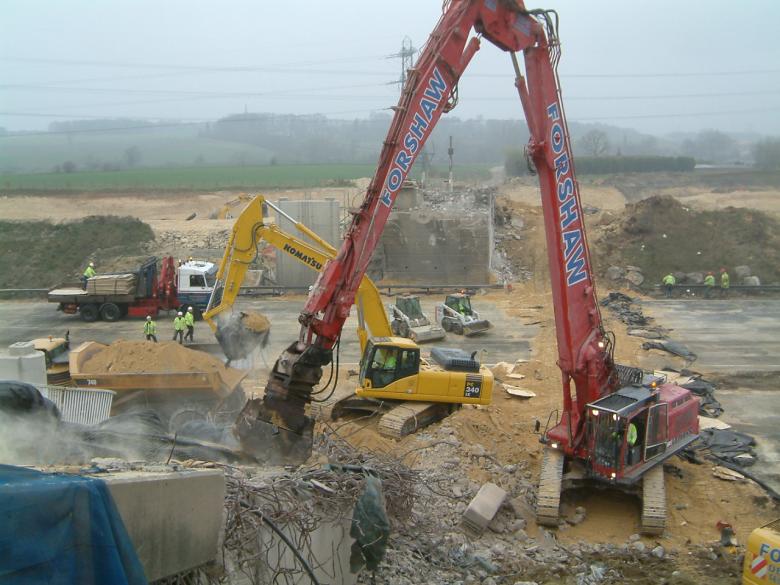
09.00 Long Reach excavator trimming off reinforcement and tendons on the deck section on the embankment.

10.00 Balmer Lindley installing barriers + road sweeper clearing the lanes.
As soon possible at the end of the road closure traffic management was installed in the central reservation area to create two running lanes each way. RMG (Balmer Lindley) carried out the reinstatement of the safety barriers in the in front of the new remainder of the bridge on the West and East bound sides of the M62. The highway drainage was also inspected to ensure that it has not become blocked – this would have been more of an issue if the weather had been poor during the clear up operation.
Following inspection of the M62 by RMG and WFL, the M62 carriageway was cleaned by road sweeper and passed fit to return to service. The traffic management once confirmed that all subcontractors are complete, was lifted at 11am and road re-opened to traffic.
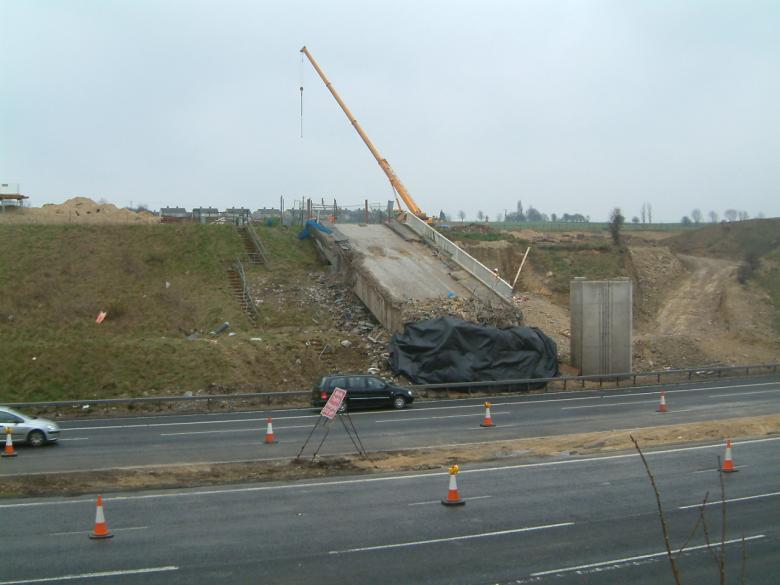
11.00 M62 Open to traffic two lanes in either direction.
Possession 2 - Side span and abutment Demolition.
The road closure of the M62 took place between -
Saturday 2nd April 2005 @ 19:00 to Sunday 3rd April 2005 @ 07:00 - The closure lasting 12hrs in total.
At the start of the M62 closure - RMG Traffic Management checked to ensure that a route is available from both Jun 32 & Jun 33 for emergency vehicles during the course of the M62 closure.
At 19:00 RMG traffic management closed off the M62 at Ferrybridge Jun 32 and at Glass Houghton Jun 33 – routing traffic via the agreed diversion route shutting down both the East and West bound M62 between the junctions.
Setting up the Traffic management took about 15 -20 mins. Once in place the RMG Traffic officer putting the diversion route place contacted the RMG site manager (David Millar) and give authorisation to start the possession. Traffic Police (Supplied by West Yorkshire Police) were located at the junctions on to the M62 (No 32 & No 33) to ensure that the traffic followed the diversion fully.
Three mobile lighting towers were positioned approximately 35m either side of the bridge to provided for the illumination of the bridge.
20.00 - Sand layer being laid over plywood and geotextile carriageway protection.
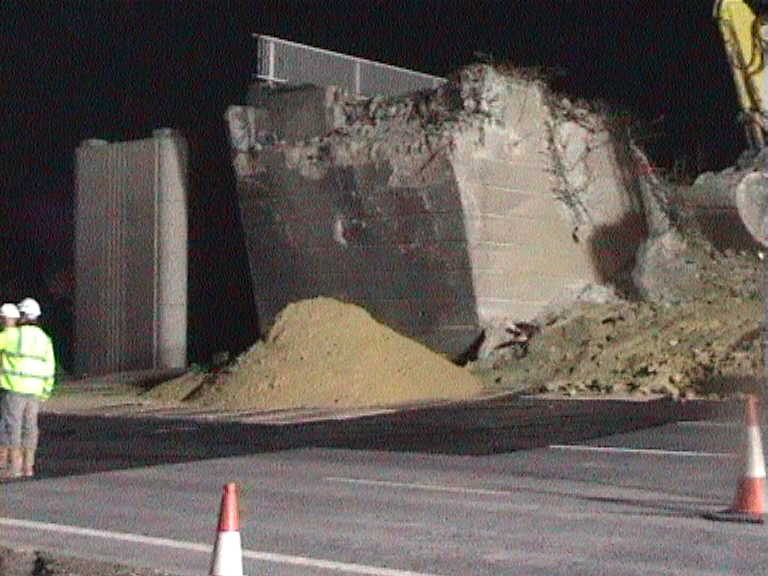
20.00 - Sand layer being laid over plywood and geotextile carriageway protection.
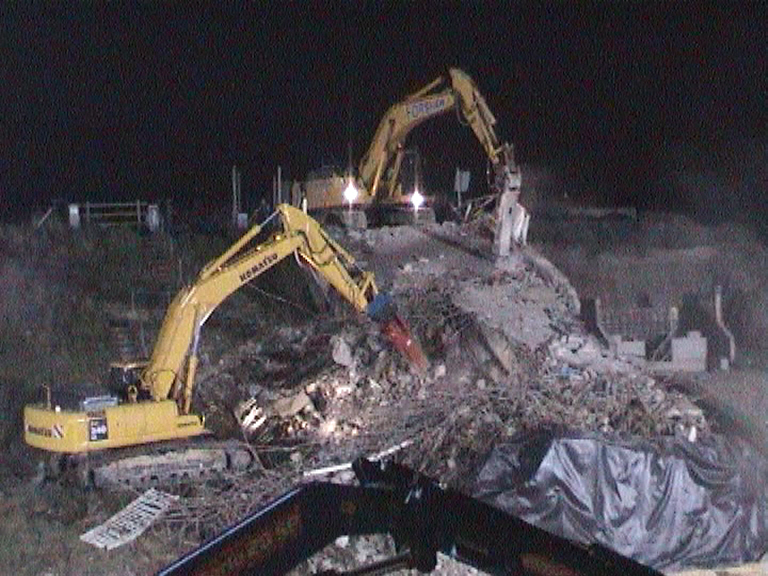
03.00 - Bridge being ripped apart on the embankment.
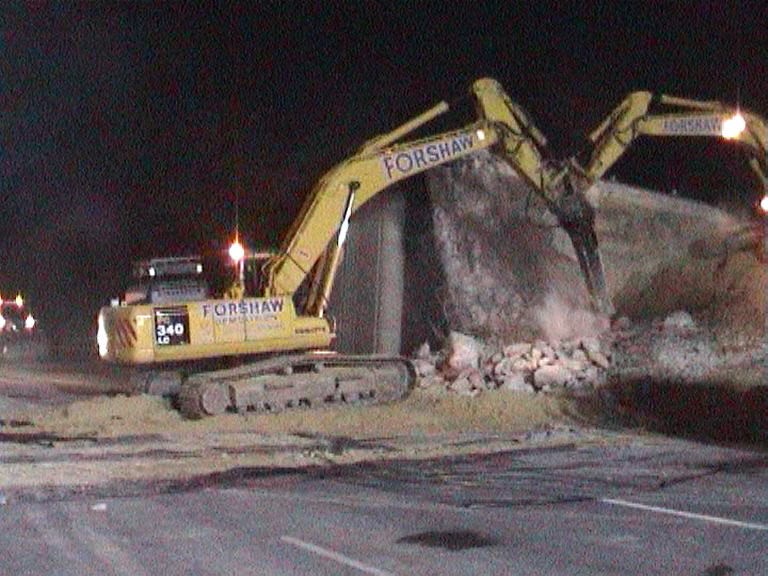
03.00 - Abutment being broken down and cleared.
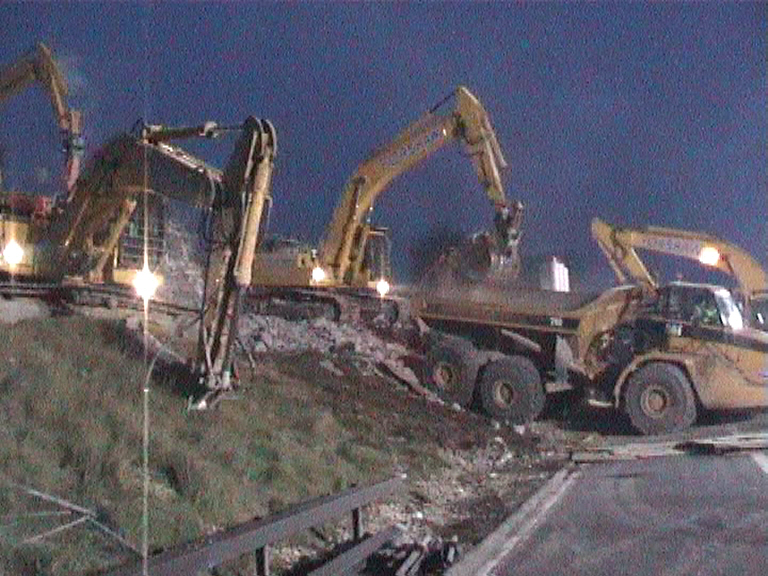
05.00 - Bridge deck being cleared on the embankment.

07.00 - Safety Barrier set up and road cleared ready to be reopened.
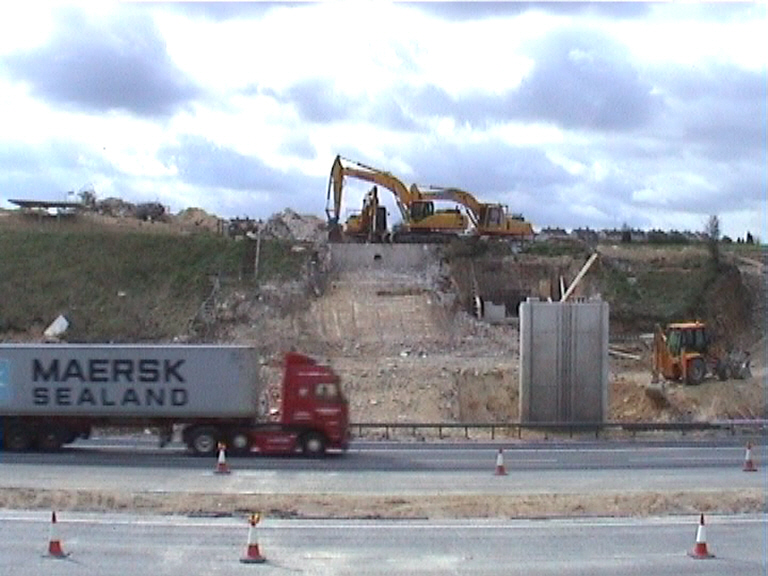
The embankment being cleared of material during normal working.
|